In today’s competitive job market securing a role as process engineer requires more than just a degree and a technical skills. It requires preparation and a deep understanding of the field. Interviewers often ask a combination of technical, behavioral and situational questions to evaluate the candidate. Here in this article we will discuss top 20 Process Engineer Interview Questions with answers.
Related: Importance of Programming and Coding in Chemical Engineering
Related: Chemical Engineering as a career option in India
Preparing for a process engineering interview requires wide range of technical knowledge, problem solving abilities and interpersonal skills.
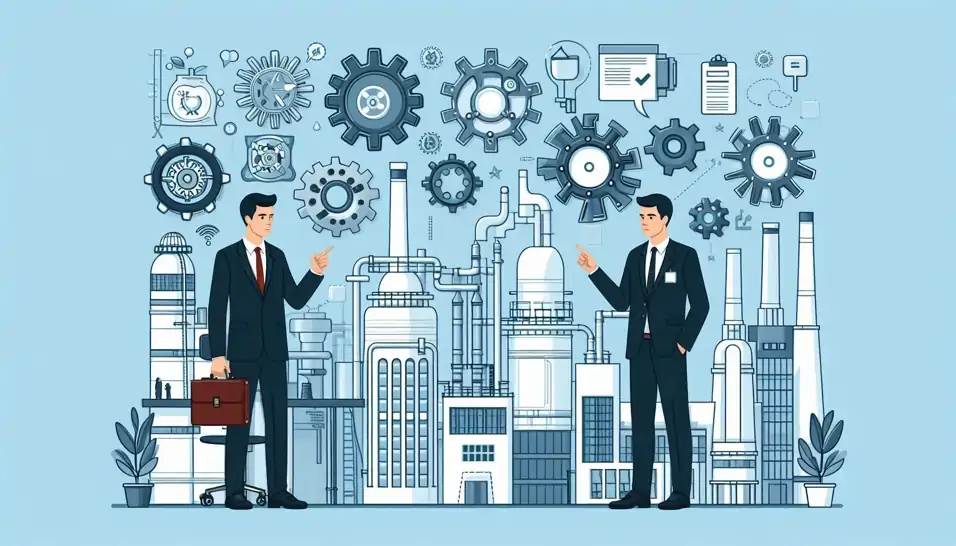
Job Role of a Process Engineer
The Job role of a Process Engineer is to to design, implement and optimize industrial process to enhance the quality, efficiency and safety of the overall process. Their expertise is important in various industries, including manufacturing, pharmaceuticals, and oil and gas, where they are responsible for smooth processes run and meet regulatory standards.
Here I am adding the list of companies hiring process Engineers, career pages are redirected.
Sector | Company | Career Page |
---|---|---|
Chemical Industry | BASF | BASF Careers |
Dow Chemical | Dow Careers | |
SABIC | SABIC Careers | |
Oil & Gas | ExxonMobil | ExxonMobil Careers |
Chevron | Chevron Careers | |
Schlumberger | Schlumberger Careers | |
Pharmaceuticals | Pfizer | Pfizer Careers |
Johnson & Johnson | Johnson & Johnson Careers | |
Merck & Co. | Merck Careers | |
Food & Beverage | Nestlé | Nestlé Careers |
PepsiCo | PepsiCo Careers | |
Coca-Cola | Coca-Cola Careers | |
Energy | Siemens Energy | Siemens Energy Careers |
General Electric (GE) | GE Careers | |
Schneider Electric | Schneider Electric Careers |
Process Engineer Interview Questions – Technical
Explain the concept of Six Sigma and its relevance to process engineering.
Six Sigma is a data-driven methodology which is focused on improving the quality by identifying and eliminating defects and minimizing variability. The aim of this method is to achieve near-perfection and follows the DMAIC framework—Define, Measure, Analyze, Improve, and Control—to systematically enhance process performance.
Also Read: Read out our full article on Crucial Role of Chemical Engineering in Everyday Life
In process engineering, Six Sigma is relevant because it helps optimize processes, reduce waste, improve efficiency, and ensure consistent quality, ultimately leading to cost savings and increased customer satisfaction.
Can you describe your experience with process simulation software?
I have extensively used Aspen Plus and HYSYS to model chemical processes and optimize plant performance. These tools allow me to simulate different process scenarios and helps in predicting the behavior of complex systems. By doing so, I can identify opportunities for efficiency improvements before implementing changes on the plant floor.
How do you approach troubleshooting process-related issues?
One of the way is to analyze the process by collecting data, identifying deviations from normal operation, and using root cause analysis tools like Fishbone diagrams or the 5 Whys technique. Once the root cause is identified, I then apply corrective actions and monitor the process to ensure the issue is resolved.
Also Read: Performance Equation for Ideal Batch Reactor
How do you ensure safety and compliance in process design?
By following industry standards, conducting hazard analyses like HAZOP, implementing safety controls and procedures, and ensuring all designs meet regulatory requirements. Regular training and safety audits are also part of maintaining a safe process environment.
Can you explain the concept of heat transfer and its applications in process engineering?
Heat transfer involves the movement of heat energy from one medium to another. This subject is essential in maintaining process temperatures, designing heat exchangers, and improving energy efficiency.
Understanding conduction, convection, and radiation principles helps in designing effective thermal management systems within chemical processes.
Related: Heat Transfer through Convection Calculator – Newton’s Law of Cooling
How do you stay updated with the latest advancements in process engineering?
I stay updated by reading industry journals, attending conferences, participating in professional networks, and taking online courses.
1. Journals such as Chemical Engineering Journal, Journal of Process Control, and AIChE Journal.
2. Articles from Chemical Engineering Progress (CEP), published by the American Institute of Chemical Engineers (AIChE).
How do you manage and analyze process data?
Data can be analyzed through statistical tools and software like Excel, Minitab, and PI System for data analysis and decision-making. This tools can collect, organize and interpret data to identify trends, optimize processes, and troubleshoot issues.
Explain the concept of mass balance in process engineering.
Mass balance is the fundamental principle used for designing and analyzing processes. This concept ensures that the mass entering a system equals the mass leaving, accounting for accumulation and reaction within the system.
How do you approach the scale-up of a process from lab to production?
From Lab Scale to Large scale production, it is required to conduct pilot tests to address scale-up challenges, such as heat and mass transfer limitations. It ensures consistent performance and safety involves careful planning, data analysis, and iterative testing to replicate lab results on a larger scale.
What methods are used for process control and automation?
In general PID controllers are used for maintaining process variables at setpoints, DCS systems for centralized control and monitoring, and SCADA for real-time data acquisition and control. These tools help in maintaining stable and efficient process operations.
Describe a time when you improved a process. What was the outcome?
Yes, I improved a heat recovery system at a chemical manufacturing plant by installing a more efficient heat exchanger. After conducting an analysis with Aspen Plus and selecting a suitable advanced heat exchanger, we integrated the new equipment into the existing system.
This upgrade led to a 20% increase in heat recovery efficiency, resulting in substantial energy savings and reduced operational costs. Additionally, the improved system helped decrease the plant’s carbon footprint, aligning with our sustainability goals.
Can you discuss a time when you had to work with a cross-functional team?
Yes, I worked with R&D, production, and maintenance teams to develop and implement a new production process. My collaboration was key to addressing different perspectives and ensuring the process met technical, operational, and safety requirements.
Also Read: Newton’s Law of Viscosity Calculator
Also Read: Other Fluid Mechanics Calculator
What strategies do you use for continuous improvement in processes?
By using Lean principles, Six Sigma methodologies, and regularly reviewing and refining processes. Scope of improvement is always there by identifying inefficiencies, implementing changes, and monitoring results to drive ongoing enhancements.
Describe your experience with project management in your industry?
In my previous role, I managed a project to upgrade a distillation unit at a chemical plant. I coordinated with a multidisciplinary team, developed a detailed project plan, and used project management software to track progress. We completed the project on time and within budget, achieving a 15% increase in efficiency and improved product quality.
Describe a situation where you had to troubleshoot a process failure. How did you handle it?
In my previous plant, chemical reactor’s output quality dropped unexpectedly. I collected and analyzed process data and found the temperature control issue. I conducted a root cause analysis and found a faulty sensor. After replacing the sensor and recalibrating the system, the reactor’s output quality returned to normal.
How did you handle a situation where a new process design did not perform as expected?
yes, I worked on designing a new mixing process for a specialty chemical. In the initial trials inconsistent mixing results were seen. Therefore, I analyzed the process parameters and found the mixing speed and duration needed adjustment. After several iterations and testing different speeds and durations, we achieved consistent and homogeneous mixing, resulting in a 20% improvement in product quality.
Describe an instance when you had to ensure compliance with environmental regulations in a manufacturing process.
While working on a project to expand our plant’s capacity, I reviewed the new process design for environmental compliance. I identified potential air emission issues and implemented additional scrubbers to control VOC emissions. I also ensured all changes were documented and reported to the environmental regulatory body. Subsequent audits confirmed we were fully compliant, avoiding any potential fines and supporting our sustainability goals.
Can you describe a time when you had to work under pressure? How did you handle it?
During a plant shutdown, I was tasked with troubleshooting a critical equipment failure. I prioritized tasks, maintained clear communication with my team, and worked extended hours. We successfully fixed the issue within the tight deadline, minimizing downtime.
How do you prioritize your tasks when you have multiple deadlines?
I use a priority matrix to assess the urgency and importance of each task. For example, during a period with several overlapping deadlines, I focused on the critical path tasks first and delegated where possible. This approach ensured that all projects were completed on time without compromising quality.
Can you tell me about a time you made a mistake and how you handled it?
I once overlooked a minor calibration error in a new process setup. Upon realizing the mistake, I immediately notified my supervisor, corrected the error, and implemented a double-check procedure to prevent future occurrences. This transparency and corrective action maintained trust and process integrity.
Preparing for a process engineer interview requires a solid understanding of both technical and behavioral aspects of the role. We’ve discussed the top 20 interview questions that you might encounter, covering areas like process design, optimization, troubleshooting, teamwork, and project management.
Edition: 9th Edition, By: Don W. Green, Marylee Z. Southard
The ultimate resource for chemical engineering, covering core concepts, data, and insights. An invaluable reference for students, engineers, and industry professionals.
Buy on AmazonFinal Tips for Interview Preparation
- Research the Company: Understand their processes, products, and industry challenges. Tailor your answers to show how you can add value to their specific needs.
- Practice Common Questions: Rehearse your answers to both technical and behavioral questions. Be clear, concise, and confident.
- Showcase Relevant Experience: Use specific examples from your past work to illustrate your skills and achievements.
- Prepare Questions: Have thoughtful questions ready for your interviewers about the role, team, and company culture.
- Stay Updated: Keep up with the latest trends and advancements in process engineering to show your commitment to continuous learning and improvement.
By thoroughly preparing and understanding what interviewers are looking for, you can confidently present yourself as a strong candidate and increase your chances of landing your desired process engineer role. Good luck!
Resources
- Indeed: Process Engineer Interview Questions– Find a variety of questions and tips on Indeed.
- Glassdoor: Process Engineer Interview Questions – Explore questions shared by candidates on Glassdoor.
- Workable: Process Engineer Interview Questions – Access a comprehensive list of questions on Workable.
- Zippia: Common Process Engineer Interview Questions – Review common interview questions and answers on Zippia.
Disclaimer: The content provided here is for educational purposes. While efforts ensure accuracy, results may not always reflect real-world scenarios. Verify results with other sources and consult professionals for critical applications. Contact us for any suggestions or corrections.
best chemenggcalc.com